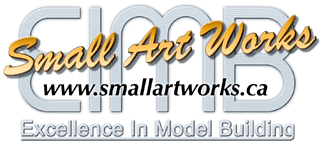
A
Resin Model Kit Primer
A
basic guide to building Small Art Works kits
If
you are
already familiar with making resin and composite model kits, you can
ignore
this article. However, if you are new to the hobby, and are only
familiar
with building the commercial injection molded styrene models that have
been the mainstay for so many years, you may find some tips here that
will
help you to get the most out of your new kit from Small Art Works. Even
if you've built some resin or composite kits before, read through this
anyway, as you may discover some techniques that you hadn't thought of
before.
OVERVIEW
The model kits
available
from Small Art Works and others like it are generally referred to as "Garage
Kits". This term has been coined to represent the fringe of the
model
kit manufacturing community (generally individuals) who produce kits
(yes,
sometimes in their garage!) that number in dozens, rather than
the hundreds or thousands or millions that constitute the bulk of
consumer-oriented
commercial model kits sold at regular retail outlets.
These
Garage kits
may, at first glance, seem terribly crude compared to the mainstream
polystyrene kits
you may be more familiar with. The reason for this is simple. Garage
Kit
manufacturers are rather low key and do not have a lot of money at
their
disposal for a multi million dollar machine shop to produce expensive
steel
molds (commercial kit molds can cost half a million dollars to produce)
and the other high tech equipment and staff used to produce mass market
kits on a very large scale. Instead, Garage Kit manufacturers use silicon
rubber molds and urethane resin to produce the parts for
the
kits like the ones available here. This process allows for lower
startup
costs than the injection molded production runs the big companies use,
but it also allows Garage Kit manufacturers to produce more specialized
products with much smaller production runs that would be impractical
for
the mainstream companies. This is a good thing, because it allows the
enthusiast
to buy kits that would not normally be available if left up to the
usual
large manufacturers. Yes, the Garage Kits are rather expensive
part-for-part
when compared to the mass produced ones available at department stores,
but that's the price paid for having a kit available that's more
suitable
for your particular interest. Also, Garage kits are more labour
intensive
on an individual basis, and the materials are more expensive per kit
when
compared to the mass-produced examples.
IN
THE BEGINNING
First, the
model the
kit is based on was extensively researched to the point where an
accurate
master pattern of the model could be made. This master
pattern was
built completely by hand, keeping in mind that the law of gravity and
physics
of fluids would play a part, and a rubber mold of this master would
have
to be made. The completed pattern was then covered in a silicone rubber
compound, which begins as a thick gooey liquid that, when a catalyst is
added, hardens around the master. After about a day, the flexible
rubber
mold was then removed from the pattern and casting of the resin copies
were then made from urethane resin. Urethane resin is a two part liquid
that, when combined, reacts to form a solid compound. The mold was
prepared,
then a quantity of resin was mixed and poured into the mold. Within a
few
minutes, the copy of the master becomes solid, and can be removed. The
resulting pieces are the parts of the model that are made into a kit.
All
of this is done by hand, one piece at a time, making the production run
fairly labour intensive and time consuming.
This
process replicates
very accurately the original master model down to the last detail, but
the casting process usually introduces some flaws, such as air bubbles,
"flash" and spillover along the mold separation lines or edges.
Sometimes
some excess resin has "heaped" at the top of the mold where it was
poured.
You must sand this flash before the parts can be assembled into the
final
unit.
KIT
PARTS PREPARATION
As a consumer,
you will
have to pay more attention to the preparation of the parts with a
Garage
Kit than you would an injection kit. There are flaws that you will have
to fill, trim and sand before you begin the assembly of the kit.
Trimming
some of the "positive" bubbles, which look like small bumps on the surface, is easy. Usually they can be picked out
with the end of a knife. To fill "negative" bubbles, you can use
standard
modeling or automotive putty, or you can use medium or
thick
grade cyanoacrylate, or "CA" (superglue) and a little accelerator.
Cyanoacrylate is the "official" name given to what you would normally
call
superglue. First, using an eye dropper or similar tool, apply a bit of
accelerator to the inside of the bubble, allow to dry then apply a drop
of CA to fill the cavity, Then more accelerator if necessary. For some
problem areas, you can apply the CA like this in layers to build up the
surfaces. When hardened, the superglue sands pretty much like the resin
the kit is made of. Use a small file to remove most of the material and
then finish with fine sandpaper. If any resin parts are warped or bent,
you can heat them with a hair dryer or hot water and slowly flex them
back
into the correct shape. Use patience and work slowly to avoid breaking
the parts. If the parts break, they can be glued back together using
the CA.
ASSEMBLING
THE KIT
Assembly of
the resin
parts of a kit can be done using epoxy or the CA adhesive mentioned above. I recommend the
better quality CA that can be purchased at your local hobby shop,
not the cheap and inferior super glues (such as the "Krazy Glue"
type
brands) available at department stores. There are three different
grades you should know about. The thick grade CA flows much
like
corn syrup, and can be used for areas where large gap filling is
required
and quick setting is not necessary. The medium grade is the
most
useful. It fills tiny gaps and is just runny enough to use a bit of
capillary
action to inch into not-so-deep crevices. The thin grade (recommended for experienced modelers only) runs
like
water, and can actually be dangerous if you are not careful (never
squeeze
the bottle while looking into the spout, for example, or you will do
some
very serious damage to your eyes!). The
thin CA will bond your skin instantly. Exercise EXTREME caution when
using
the thin grade! Use the thin CA by
holding
the parts to be joined together, and then apply a TINY amount of thin
CA
to the joint. Capillary action will carry the glue into the joint,
forming
a very solid bond. It is important that you make the parts match very
closely.
The thin CA will not fill any gaps. Also note thet thin CA is very
runny
like water, so caution must be used to prevent it from running
into
areas you don't want it to. Keep a dry rag and CA debonder
handy to wipe away any spills.
Recently I became aware of an excellent CA glue called Gorilla Glue,
a superglue that is very strong and commonly available in most hardware
stores. Unlike most department store superglues, Gorilla Glue is very
high quality.
You will
also find
the use of CA accelerator (also available at your hobby dealer)
very useful. Sometimes when a joint is stubborn and will not seem to
bond,
you can force the glue to cure instantly by giving it a shot of
accelerator.
This also helps in gap filling.
IMPORTANT
SAFETY TIPS REGARDING CYANOACRYLATES
The use of
accelerator
will cause the glue to cure VERY quickly, and a lot of heat is
generated
from the chemical reaction. Sometimes, if you have a relatively large
quantity
of glue pooled in a deep cavity, the glue will often fizz, sizzle,
spit,
pop and smoke when the accelerator hits it, so you should wear eye
protection.
The escaping fumes can also be exceptionally irritating, so keep away
from
them. Provide yourself with adequate ventilation and fresh air. Also,
if
you have any of the glue on your skin which is hit by the accelerator,
it will cause very nasty burns (especially with the thin CA).
Always
exercise caution when using CA and accelerator to avoid some very
unpleasant
experiences! Remember, we want model building to be FUN!
PAINTING
Finishing and
painting
a resin model is just like the styrene kits, with one major exception.
The resin your kit is made from will take most types of enamels and
acrylic paints such as all hobby paints, spray paints and even
automotive lacquers (which damage
styrene
kits) quite nicely! But hobby paints designed for plastic model kits
still work best. Use the standard preparation techniques for all
models,
like washing the parts to eliminate greasy fingerprints and mold
release
agents. I also recommend priming all the parts before painting with an
cellulose or lacquer based primer, like automotive primer. This also
helps
you locate minute flaws before finishing. Spraying with an airbrush is
preferred, but you can use spray cans and hand brushing too.
CONCLUSION
The assembly
and preparation
techniques of urethane resin kits may seem very difficult to you
initially,
but in reality, once you understand the construction techniques and
nuances
of working with resin, you may find them just as easy as the "regular" styrene kits!
Jim
Small,
Small Art Works, jim@smallartworks.ca |